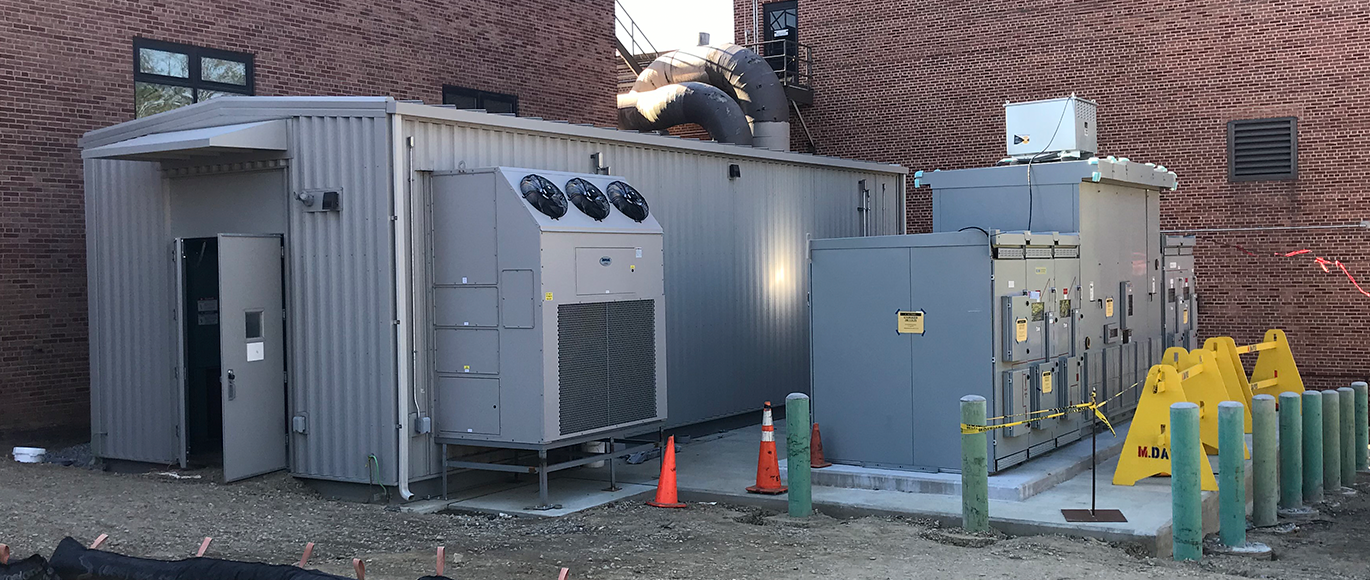
The DuPont Experimental Station located in Wilmington, DE, has been engaged in a multi-year site infrastructure improvement and building expansion program to increase the site’s central chiller plant’s 15,000 tons of refrigeration production capacity. The current plant includes four lithium bromide steam absorption chillers which contribute 6,000 tons of refrigeration. In 2019, Pennoni was awarded a full-service design and engineering contract to begin a multi-phase, multi-year capital program to replace the four existing steam absorption chillers with three new high efficiency electric centrifugal chillers. Each of the new chillers will provide 3,000 tons of refrigeration.
This project was schedule-driven to provide uninterrupted chilled water service in support of site business operations. New major equipment installation had to be accomplished during the off-season months and ready for operation by the start of the next cooling season. This limited window of opportunity required a very coordinated effort between design, construction, and DuPont site operations.
To accomplish the necessary coordination of design, long lead equipment fabrication and delivery, and field construction, a multidisciplinary project team was formed from the onset of project Front End Loading (FEL). The team consisted of Pennoni (mechanical, electrical, civil, survey, and geotech engineering from our Newark, DE office, and structural engineering from our Philadelphia office), DuPont Operations, KBR (DuPont’s resident CM), the General Contractor M Davis, the Civil contractor Eastern States Construction Services, and the equipment supplier, Johnson Controls (York International). This team has participated in ongoing value engineering meetings to mitigate design challenges, optimize design, control costs, and meet the client’s aggressive construction schedule.
This team concept was previously used, and proved to be very successful, for a 10,000-ton Cooling Tower project bounded by a similar limited off-cooling season construction schedule. Project resources were engaged from the onset of design allowing the project delivery process to prepare and deliver partial design packages in unison with the input of suppliers, fabricators, and installers to expedite the construction process. Design packages were delivered at specified intervals to allow for field construction activities to occur while ongoing operation of the chiller plant continued.
The congested nature of the existing 1950s chiller plant building presented design clearance and interference challenges. To improve and expedite the equipment layout and pipe routing tasks, a complete high definition laser scan of the building’s interior and exterior was performed. This data was compiled and used to develop 3D models of the existing conditions to determine locations of new equipment, piping, electrical systems, and structural steel.
A 20-inch diameter stainless steel cooling tower and 18-inch carbon steel chilled water supply/return piping were designed and connected to the existing piping headers. A new refrigerant exhaust fan, makeup air unit, and associated ductwork, along with pressure relief valve discharge piping from the chiller connections up through the building roof and discharging 15 feet above the roof level were also designed The system provides the required continuous and emergency ventilation to the machinery room and was connected to a new refrigerant leak detection and alarm system to provide a safeguard for personnel protection.
Due to the additional equipment and pipe support loads, some existing roof steel required reinforcement to accommodate the increased loads. Concrete equipment foundations, a new equipment access platform, support structure for rooftop equipment, and a foundation pad for a new electrical substation were all designed. A section of the external wall of the building and adjacent external column was underpinned to allow the installation of an underground electrical duct bank.
Two new 12,000-volt feeders were designed and connected the site’s main high voltage power distribution circuits to a new 5,000 kva electrical substation. The new substation, including a new transformer and switchgear, was sited just outside of the existing chiller plant building on a new concrete pad. A new pre-engineered metal building (PEMB) was designed to house the new chiller variable speed drive (VSD) and allocate space for future chiller VSDs and a pump VSD. A new underground electrical duct bank was designed to house the numerous conduits between the PEMB and the existing building. With facility aesthetics at the Experimental Station being an inherent component of the site’s historical character, Pennoni FX Studios prepared a design specific rendering of the new substation facility for approval by DuPont site leadership prior to proceeding with final selection of the siting location.
On June 1, 2020, the first 3,000-ton chiller was placed into operation, meeting the required schedule for the start of the current cooling season. The second chiller is scheduled for start-up and operation in May 2021 with the third chiller to follow as needed to satisfy the site’s growing cooling load requirements.