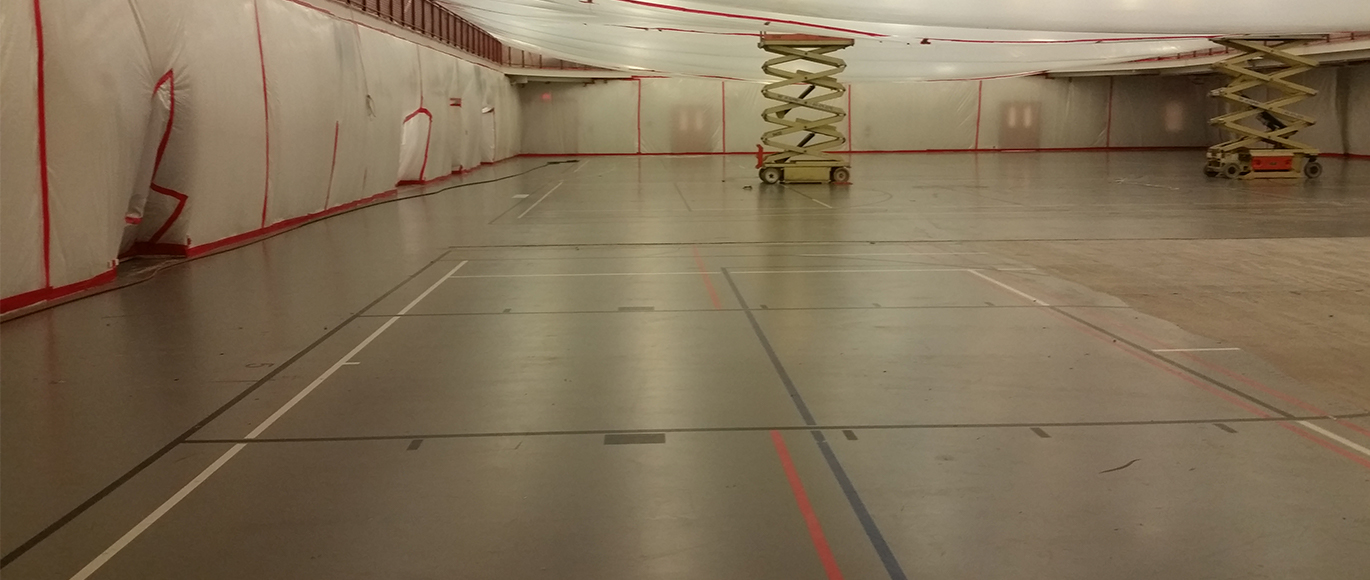
Over the past five to ten years, the confirmation of mercury in rubberized gym floors has increased significantly throughout the United States. Exposure to mercury through inhalation at elevated concentrations can lead to brain and kidney damage. Children are more susceptible to mercury exposure than adults.
In most cases, air quality risks associated with mercury flooring are mitigated by engineering controls such as encapsulation or increasing fresh air ventilation to decrease mercury vapor concentrations. However, when workers disturb the material for renovations, repair, or replacement, it can create hazardous levels of mercury.
How do you know if your flooring has mercury? What do you do about it? This article has been put together by Pennoni based on experience with various projects, our understanding of the regulations, and current industry guidelines. The information provided is based on Environmental Protection Agency (EPA), Occupational Safety and Health Administration (OSHA), and Agency for Toxic Substances and Disease Registry (ATSDR) guidelines.
BACKGROUND
Mercury is a metal that exists in liquid and vapor form. It is commonly used in many consumer products and is typically encountered in homes, schools, hospitals, offices, and industrial workplaces. In the 1960s, many manufacturers began to include mercury in their rubberized gym floor products to help keep the rubber flexible over time. According to the ATSDR, “In the 1960s, a number of companies began manufacturing and installing a thin layer of synthetic, polyurethane flooring on top of concrete sub-floors, to provide a resilient and rubberlike surface.”
“Very young children are more sensitive to mercury than adults.” – ATSDR ToxFAQs
Mercury-containing polyurethane floors were widely installed in school gymnasiums across the U.S., until being discontinued in the mid-1980s. Many of these floors remain in place today, and recent reports have demonstrated that some emit notable amounts of elemental mercury vapor, which has raised questions about inhalation health risks, particularly for children in schools.
EXISTING GUIDELINES AND STANDARDS
Most states do not currently have specific recommended exposure limits for members of the general public or children in schools for exposure to mercury. However, various federal and industry groups have published recommended exposure limits for mercury vapors:
OSHA 100 micrograms per cubic meter (ug/m3)
NIOSH 50 ug/m3
ACGIH 25 ug/m3
ATSDR 3.0 ug/m3
USEPA 0.3 ug/m3
RECOMMENDED STEPS IF YOU HAVE FLOORS SUSPECTED OF CONTAINING MERCURY
STEP 1 – Develop Sampling Plan
Prior to conducting sampling, a sampling plan should be made that should represent sampling procedures, locations, sampling media, laboratory analysis, etc. The sampling plan should be developed to identify occupied vs unoccupied or worst-case scenarios such as HVAC systems turned off, etc. The sampling plan should be developed and signed off by a Certified Industrial Hygienist. It is important to note that temperature and relative humidity directly affects the volatility of mercury and testing in winter months should likely result in lower concentrations than in summer months.
STEP 2 – Bulk Sampling of Rubberized Flooring
An industrial hygienist should collect representative full-thickness pieces of the floor for analysis at an accredited lab. Approximately a two square inch floor sample should be collected and should be analyzed using EPA 7471B to determine the amount of mercury present. If the EPA 7471B test shows that mercury in a floor is less than 1 ppm, it can be assumed that the floor was not manufactured using a mercury containing catalyst. If mercury in floor levels are greater than 1 ppm, proper floor maintenance, adequate ventilation and cooling and initial worst-case air sampling should be implemented.
If mercury is found in the flooring greater than 1 ppm, it is recommended that a toxicity characteristic leaching procedure (TCLP) Method 1311 be performed on the flooring as well. The industrial hygienist should collect an eight square inch floor sample to determine whether the floor must be disposed of in a hazardous waste landfill or can be disposed of as non-hazardous waste. Floors with leachate that exceeds the EPA maximum concentration of 0.2 ppm (mg/L) of mercury must be disposed of as hazardous waste.
STEP 3 – Conduct Mercury Air Sampling
A representative number of full-day (8-hour), samples should be collected in the breathing zone (3 feet for up to eighth grade; 5 feet for higher grades) for analysis by an accredited laboratory using NIOSH Method 6009. Sampling should be conducted using active sampling pumps. A background sample should be collected outdoors at each location. Samples should be collected for approximately 480 minutes at a calibrated rate of 0.15 liters per minute for an approximately total value of 72 liters. It is anticipated that two to four samples per gymnasium would be the minimum.
Prior to the collection of air representative air samples, a real-time Mercury Vapor Analyzer such as a Jerome J405 or J505 should be used to record instantaneous mercury concentrations. Approximately 25-30 readings should be collected at breathing zone height in a grid pattern throughout the gymnasium. The location with the highest observed reading, if any, should be selected for the air sampling test by NIOSH Method 6009. Air samples should be set up in the center of the room initially and moved as needed to adjust for the documented readings.
If elevated concentrations of mercury are identified, additional samples may be recommended in adjacent areas such as locker rooms, coach and PE offices, bathrooms, and hallways.
STEP 4 – Document in a Formal Report
Upon completion of assessment and sampling activities, a technical report should be prepared summarizing observations made during the investigation and recommendations for remediation or additional sampling. The report should include, but not be limited to; site plan, air sampling certificates of analysis, calibration documentation, photographs, and other information gathered during the project.
If you’re interested in learning more, contact:
Alan Lloyd, CIH, CSP, ENV SP
Certified Industrial Hygienist #9099CP
Certified Safety Professional #21632
Environmental Sustainability Partner #19471
alloyd@pennoni.com
Nancy Wilson, REHS, CMC
Senior Industrial Hygienist
Registered Environmental Health Specialist #B101753
nwilson@pennoni.com
This article was originally posted on LinkedIn.